Family Overview
A family of high-performance taps, engineered for a long-lasting tool life, durability, and high cutting speeds. These taps were designed to ensure that each and every thread comes out as good as the first one, and takes as little time as possible. A wide variety of tap designs and grades helps to ensure a perfect match for every application.
The tools of the family can be roughly divided into two groups: Cutting taps (which in turn can be either Spiral Fluted or Straight Fluted with a Spiral Point), and Forming taps. The rule of thumb is that if the material produces a continuous “stringy” chip, a Forming tap should be considered first.
Note: The family is known as X-treme Taps in the US market.
Supported Tap Standards:
- DIN 371: Taps with reinforced shank for metric coarse (M)/fine (MF) threads up to M10, and for UNC/UNF threads up to 3/8″ nominal diameter
- DIN 376: Taps with reduced shank diameter for metric coarse (M) and UNC threads
- DIN 374: Taps with reduced shank diameter for metric fine (MF) and UNF threads
- DIN 5156: Taps with reduced shank diameter for Whitworth pipe G threads
- JIS B-4430: Taps for JIS metric threads
This range of solid carbide taps consists of the following lines:
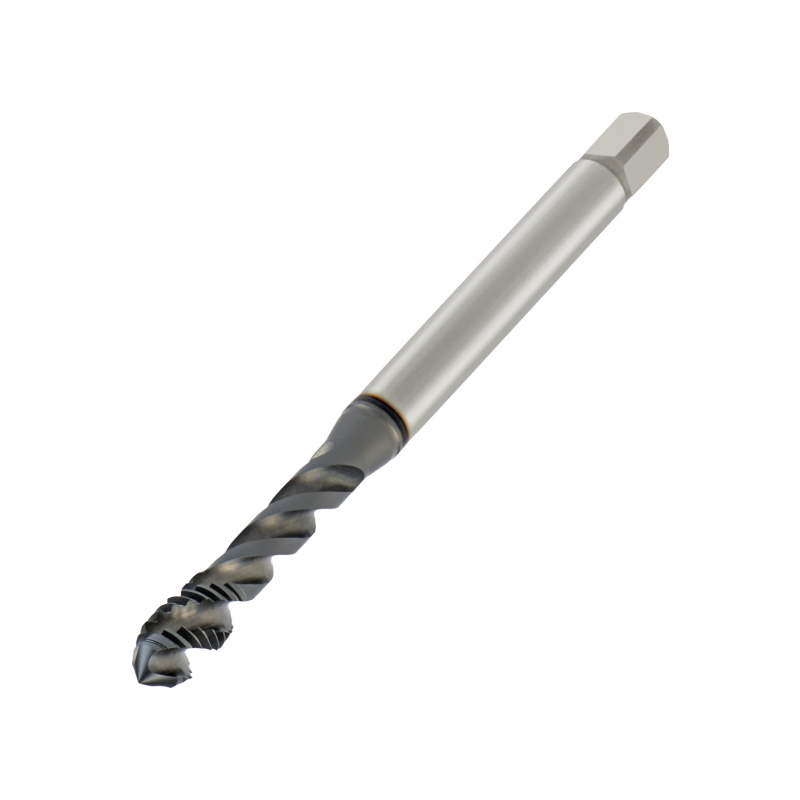
SPIRAL FLUTED TAPS
These cutting taps are suitable for threading blind hole applications. The spiral flutes drive the chips towards the shank, and out of the hole. They can’t be used for tapping through holes.
Features:
- Compatible with a large variety of materials (especially when the XT3 grade is used)
- Full thread top formation makes thread less prone to cross-threading
Carbide Grade(s):
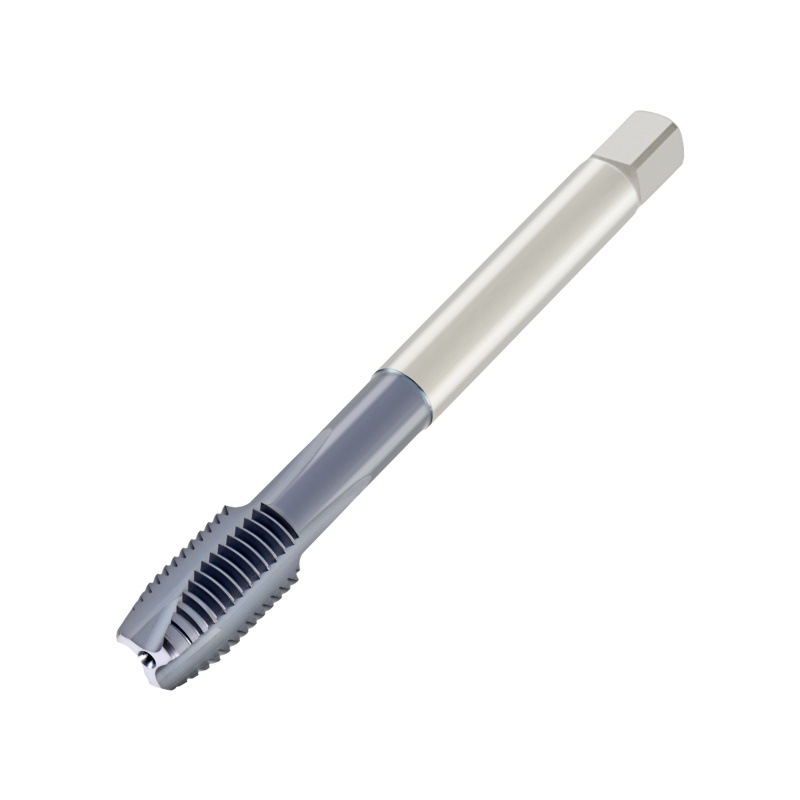
SPIRAL POINT TAPS
A range of cutting taps with straight flutes and a spiral point, which drives the chip in the direction of the feed. This makes these taps ideal for threading through hole applications, as the chips will be evacuated through the hole.
At the same time, their design makes these taps unsuitable for blind hole jobs. Moreover, when tapping a through hole, the tap must go through until the spiral point passes the hole.
Features:
- Compatible with a large variety of materials (especially when the XT3 grade is used)
- Full thread top formation makes thread less prone to cross-threading
Carbide Grade(s):

FORMING TAPS
Forming taps create the thread through plastic deformation, rather than cutting. They are capable of machining both both blind and through holes, but their use is limited to ductile materials.
These taps are ideal when chip-free machining is required for some reason. Note that the bore diameter required for forming taps is greater than the bore diameter needed for cutting taps.
Features:
- No chips or issues with chip evacuation
- Capable of tapping at higher speeds than cutting taps
- Lack of flutes, and a larger core make for stronger tools
- Longer tool life and smoother thread finish (as compared to cutting taps)
Carbide Grade(s):