
The famous Vulcan greeting from Star Trek takes on a whole new meaning when it comes to tool life. This was recently proven at Apex CNC Swiss, a machine shop specializing in high precision complex parts machined from hard materials and alloys. According to Chuck Fluharty, co-owner of Apex, “We were machining an electronics circuit board standoff in 303 stainless on a Star SR-20R III machine. The part required a 4.6 mm (0.180″) deep hole threaded with a 0-80 UNF thread. At the time, we were working with tooling from a well-known German maker that delivered 200 to 300 parts before tool failure. We did not feel that this was acceptable and, when we contacted the manufacturer’s technical support, they advised that that performance was ‘normal.’ We immediately began to look for an alternative.”
Production rises to more than 2,000 parts
When Chuck and his team tried the Carmex mini mill-thread design, they saw production rise to more than 2,000 parts. More than that, they completed a further 500 parts in 17-4 stainless prior to failure.
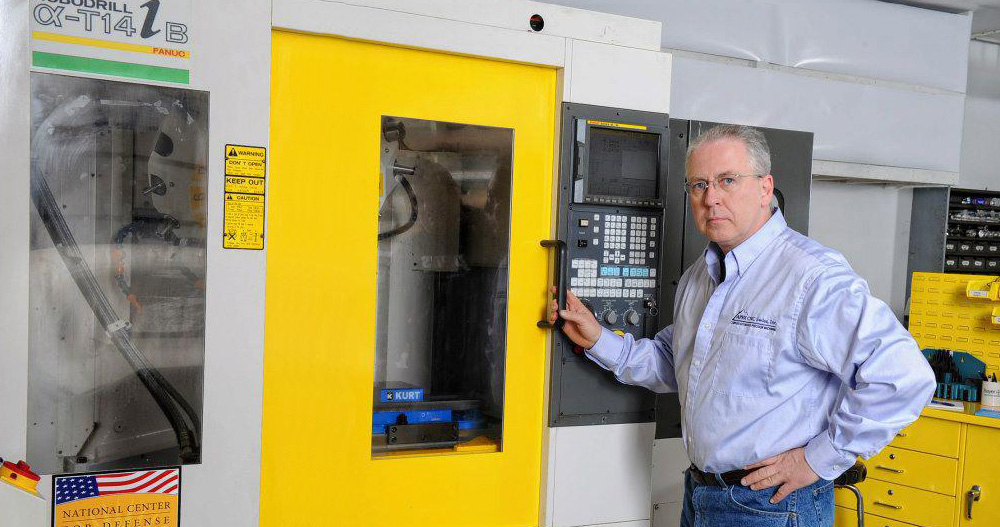
“Longer tool life means more than saving money buying replacement tools. When we realized what the Carmex tool could do, it freed us up from monitoring the machine and changing tools — and that resulted in additional savings in time and man-hours.”
Additional savings in time and man-hours
Carmex performance at Apex CNC Swiss is another example of how tooling engineered for high performance and long life leads to greater prosperity for the customer. “Live Long and Prosper.”